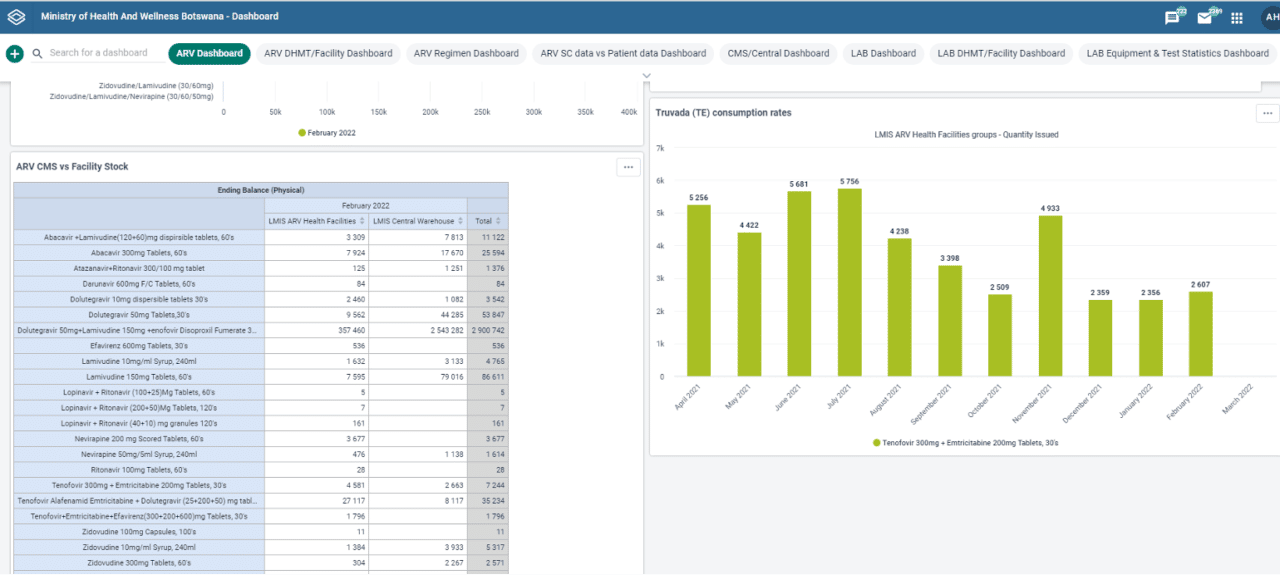
Adapting the Existing DHIS2 to Support Supply Chain Decision Making in Botswana
The USAID Global Health Supply Chain Program worked with Botswana’s Ministry of Health to integrate supply chain data into the national HMIS, providing a cost-effective solution that has helped prevent treatment interruptions
In Botswana, the Ministry of Health (MoH) and other supply chain actors had a wealth of data from many sources, including the Warehouse Management System, Excel-based monthly LMIS reports, data from the Quantification Analytics Tool (QAT)5, monthly patient reports, and others. Health facilities did a good job reporting stock levels and other key data. Yet, the lack of integration of all the systems required manual workarounds and made it difficult to analyze and leverage all data for decision making to ensure a reliable supply of health commodities at the last mile. Also, since most tools were standalone and not interoperable, data were accessible only to a few users. The existing tools generated reports that needed further analyses and interpretation.
After careful analysis and consultation with the MoH and other stakeholders, the USAID Global Health Supply Chain Program – Procurement and Supply Management project (GHSC–PSM) launched an initiative in March 2021 to integrate the various data platforms in Botswana’s DHIS2. and create new dashboards to help supply chain managers to make decisions about procurement, redistribution of commodities between health facilities, and other actions.

Instead of introducing new software, the MoH preferred to integrate and enhance DHIS2 because MoH staff were already familiar with it. For the last several years, DHIS2 has been used in the country for monthly reporting on ARVs, prevention of mother-to-child HIV transmission, malaria programs, and MoH surveys and surveillance activities, but had not been used as a platform for supply chain management. DHIS2 is also being used for several COVID-19-related activities, including surveillance and vaccination reporting. Importantly, the system is open-source and the Botswana government already owned and managed a server dedicated to operating it. Leveraging the existing resources rather than developing new software saved resources and reduced the need to retrain supply chain workers.
“We might have done this earlier if we had completely understood DHIS2’s capabilities and applications to supply chain management. Once you get to know it better, you realize that it can be customized and has tremendous potential for data storage and reporting, and display of data analytics and visualizations.”
Ashenafi Desta Hordofa – Logistics Management Unit Manager, GHSC–PSM
To create the new dashboards focused on supply chain management, GHSC–PSM contracted with a software company recognized for its extensive experience working with DHIS2. The company deployed a small team of five who made all the necessary changes by 2021. Since then, at monthly technical working group discussions with the central medical store (CMS), GHSC–PSM, USAID, several non-governmental organizations, and other key partners, supply chain managers have used the powerful new dashboards and data visualizations to identify risks to commodity availability at all levels of the supply chain, including the last mile. The system includes all commodities in Botswana’s public health system. A common discussion point concerns the current stock situation at CMS and, if stocks of a commodity are low, planning for stock redistribution from health facilities with excess stock to those at risk of stockout until deliveries arrive to replenish the CMS. CMS also uses the analysis in the dashboards to decide on the quantity of stocks to replenish health facilities.
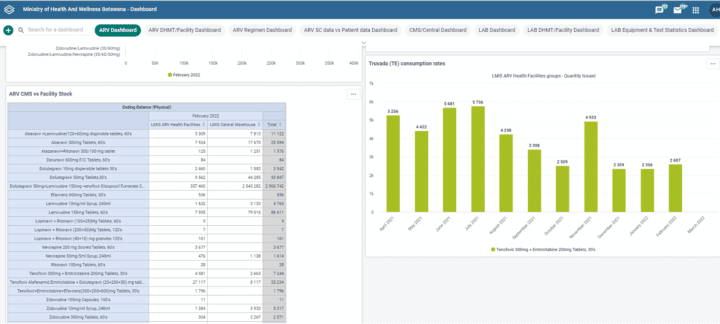
The enhanced decision-making process has already contributed to helping manage stocks of legacy ARVs during the transition to new adult and pediatric HIV/AIDS treatment regimens. Triangulation of patient data with supply chain data has been especially useful in managing this transition: supply chain managers could analyze maps, tables, and charts showing stock levels at all levels of the supply chain, consumption rates of new and legacy ARVs, and numbers of patients transitioned into new regimens. In this way, supply chain managers redistributed stock between treatment sites to ensure a reliable supply of legacy ARVs and avoid costly unnecessary procurement as the new regimens replaced the old. ARV stock levels were already adequate before the intervention and have been maintained. Between April 2021 and February 2022, the monthly percentage of health facilities where tenofovir, lamivudine, and dolutegravir stock was available ranged from 97 to 100 percent (monthly average of 98 percent since 2018). Pediatric dolutegravir 10 mg was introduced around June 2021, and the monthly percentage of health facilities where it was available also ranged from 97 to 100 percent until February 2022.
The key impact of the tool so far has been providing online visibility of stocks at the facility level, helping CMS with stock redistribution, particularly for products that are often stocked out at the CMS level, and therefore avoiding treatment interruptions. In contrast to the situation for ARVs described above, the stock levels of most health commodities are currently low mainly because of delays at CMS to renew long-term procurement contracts. With the low stock levels, the dashboard is greatly helping CMS to redistribute the limited stocks to avoid treatment interruptions. For example, the CMS is using the supply chain dashboard to locate and consolidate the drugs and supplies from other health facilities for redistribution during an ongoing cataract surgery campaign in Serowe-Palapye District Health Management Team. Overall, the initiative has proved to be a cost effective and rapid solution, less expensive than previous large technology initiatives. The development of the tool amounted to almost $55,000, with development and rollout taking eight months, and it is an open-source software with zero subscription fee. A comparable tool with similar functions, such as Microsoft Power BI, would cost about $5,000 of monthly subscription fee, and a more robust eLMIS solution would cost more than $2 million. Since funding to invest in an eLMIS was lacking, DHIS2 allows at least the ability to consolidate the manual reports through automatic uploads, run analytics, and share data using a web-based platform.
However, despite the initiative’s overall success, some challenges have emerged, including technical glitches typically related to software development and connectivity challenges when accessing a new online platform. The most pressing issue has been the impact of moving large amounts of data to the MoH server, resulting in slower than usual processing. GHSC–PSM is working with CMS to expand server capacity. For those considering similar adaptations to DHIS2, especially in the absence of other eLMIS solutions, Ashenafi Desta Hordofa, Logistics Management Unit Manager, GHSC–PSM, encourages exploring the full potential of the platform. “We might have done this earlier if we had completely understood DHIS2’s capabilities and applications to supply chain management. Once you get to know it better, you realize that it can be customized and has tremendous potential for data storage and reporting, and display of data analytics and visualizations.”
This article is adapted from the technical report “Driving Last-Mile Solutions to Ensure Access to Public Health Commodities,” and is republished with the permission of GHSC-PSM.